Abattoir flooring is a critical component in ensuring the efficient and hygienic operation of meat processing plants. The choice of flooring in an abattoir can significantly impact the facility’s cleanliness, worker safety, and overall functionality. Among the various options available, Concrete Flooring, Epoxy Resin Flooring, Rubber Flooring, Vinyl Flooring, and Tile Flooring are popular choices. However, when it comes to the best choice for abattoir flooring, Tile Flooring and Stainless Steel Flooring stand out due to their exceptional properties.
Advanced Tile Flooring for Abattoirs: Acid-Resistant, Slip-Proof, and Hygienic
Tile Flooring in abattoirs is not just a practical solution but a technologically advanced one, especially when considering the hostile environment of meat processing facilities. The acid resistance of these tiles is a critical feature, as abattoirs often use strong cleaning agents and deal with organic acids from meat processing. The tiles are manufactured using materials that are non-reactive to a wide range of acidic substances, ensuring longevity and maintaining surface integrity even under constant exposure to these harsh chemicals. Moreover, the chemical resistance of these tiles extends beyond just acids; they are also resistant to alkalis, solvents, and other industrial chemicals commonly found in abattoir environments. This robust resistance protects the flooring from degradation, thus preventing the need for frequent replacements and reducing long-term maintenance costs.
The slip-resistance of tile flooring in abattoirs is another vital technical aspect. These floors are often exposed to wet and slippery conditions, making slip resistance a top priority for worker safety. The tiles are designed with a textured surface that provides increased traction underfoot, significantly reducing the risk of slips and falls. This texturing is achieved through various surface treatments or by incorporating materials that naturally provide grip, even when wet. Additionally, tile flooring in abattoirs is engineered for high levels of hygiene. They are often treated with antimicrobial agents that inhibit the growth of bacteria, molds, and fungi, essential in maintaining a sterile environment crucial for meat processing. This hygienic property is complemented by the ease of cleaning and sanitizing tile floors, ensuring that they can be effectively cleaned with minimal effort.
Furthermore, the temperature resistance of these tiles makes them an exceptionally versatile option for different zones within an abattoir. They can withstand extreme temperature variations, which is essential for areas like freezers and hot washdown zones. This property is due to the thermal stability of the materials used in tile manufacturing, which do not crack or lose integrity when subjected to sudden temperature changes. Such durability is crucial in abattoirs, where floors must endure not only thermal shocks but also the weight and movement of heavy machinery and equipment. This combination of acid resistance, chemical resistance, slip resistance, hygiene, and temperature resistance makes tile flooring an unparalleled choice for abattoirs, providing a safe, durable, and sanitary environment that meets the rigorous demands of the meat processing industry.
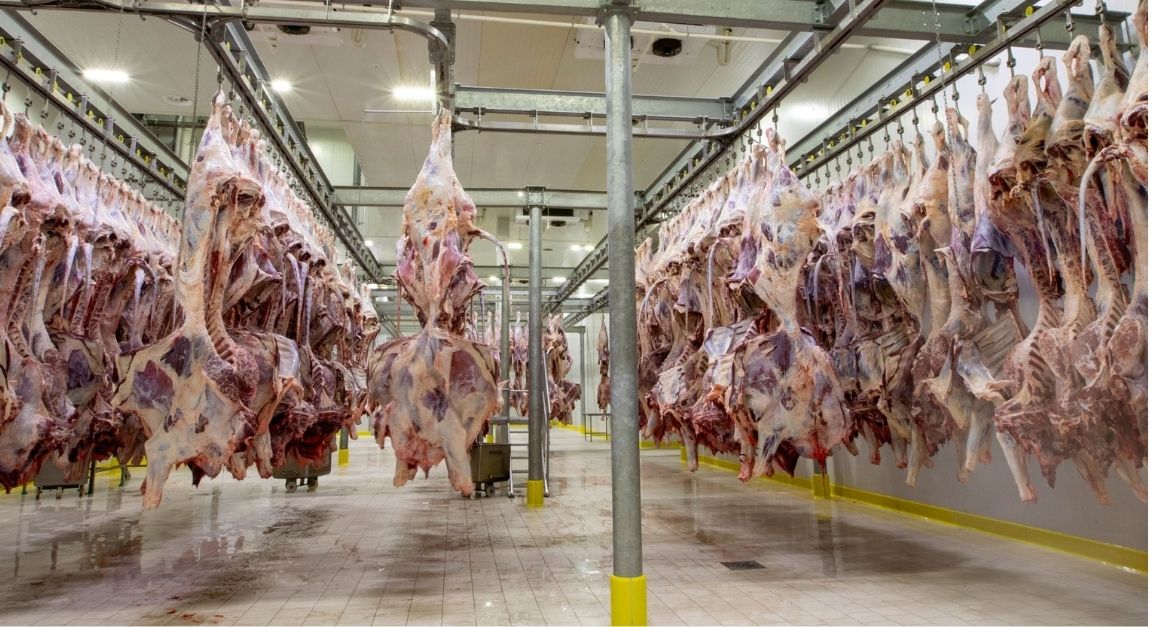
Stainless Steel Flooring: Durable, Hygienic, and Safe for High-Traffic Abattoir Zones
Stainless Steel Flooring stands out as an exceptional choice for abattoir flooring, particularly in areas demanding high durability and supreme hygiene, such as cold room door passages. The inherent properties of stainless steel make it ideal for withstanding the harsh conditions of these high-traffic zones. Its robust construction ensures resistance to the heavy impact and frequent movement of equipment, a common scenario in abattoirs. Additionally, stainless steel’s non-porous surface is impervious to stains and is remarkably easy to clean, a crucial feature for maintaining stringent hygiene standards in meat processing facilities. This ease of cleaning is enhanced by the material’s resistance to common cleaning agents and disinfectants, ensuring that the floor remains sanitary without degrading over time. Furthermore, stainless steel flooring is resistant to corrosion, a vital attribute in environments exposed to moisture, organic materials, and various chemicals. This corrosion resistance extends the lifespan of the flooring, making it a cost-effective long-term solution. The surface of these stainless steel tiles can be textured to provide additional slip resistance, crucial for ensuring worker safety in often wet or greasy conditions. The aesthetic appeal of stainless steel, coupled with its functional benefits, makes it a modern, efficient, and reliable flooring option for any abattoir, enhancing both operational efficiency and workplace safety.
Optimize Abattoir Flooring with Vibratory Application Technique
For the installation of these flooring types, the Vibratory Application Technique is the recommended system for Abattoir/Slaughterhouse flooring. This technique involves a thorough process of cleaning the existing concrete floor, applying mortar, and then laying the Acid resistant tiles in a precise manner. High-quality adhesives ensure a strong bond, and the vibratory compression technique guarantees a flat, even surface with no gaps. This method ensures a durable, hygienic, and efficient flooring solution for abattoirs.
Vibroser Leads in Hygienic, Durable Flooring for Abattoirs and Food Processing Industries
Vibroser stands out in the industry with its specialized manufacturing of hygienic, hard-wearing, non-slip flooring solutions, catering specifically to the unique needs of abattoirs and processing areas for meat, fish, and seafood. Their products are engineered to withstand the rigorous demands of these environments, which include exposure to heavy foot traffic, harsh cleaning agents, and extreme temperature variations. What sets Vibroser apart is their commitment to quality and durability, ensuring that their flooring solutions not only meet but exceed the stringent hygiene standards required in food processing. The non-slip feature of their floors is a testament to their dedication to safety, reducing the risk of accidents in wet or slippery conditions. With a focus on innovation and utilizing cutting-edge technology, Vibroser’s flooring options offer a seamless blend of functionality and longevity, making them the preferred choice for businesses that prioritize hygiene, durability, and worker safety in their abattoir or food processing facilities. This expertise and focus on specialized solutions position Vibroser as a leader in the market, providing flooring solutions that are both practical and reliable for the demanding conditions of the food processing industry.
FAQs About Abattoir Flooring
What Makes Tile Flooring the Optimal Choice for Abattoirs?
Tile flooring is considered the optimal choice for abattoirs due to its combination of durability, hygiene, safety, and resistance to harsh environmental conditions. Here are the key reasons why tile flooring is highly suitable for abattoirs:
Acid and Chemical Resistance: Abattoirs often use strong cleaning agents and organic acids during meat processing. Tile flooring is manufactured using materials that are non-reactive to a wide range of acidic substances and industrial chemicals, ensuring longevity and maintaining surface integrity even under constant exposure to these harsh chemicals.
Slip Resistance: Safety is paramount in abattoirs, where floors can be wet and slippery. Tile flooring is designed with a textured surface that provides increased traction, significantly reducing the risk of slips and falls. This feature is crucial for maintaining a safe working environment.
Hygienic Properties: Tile flooring in abattoirs is often treated with antimicrobial agents that inhibit the growth of bacteria, molds, and fungi. This is essential for maintaining a sterile environment crucial for meat processing. Additionally, the ease of cleaning and sanitizing these floors ensures that they can be effectively cleaned with minimal effort, thereby maintaining high hygiene standards.
Temperature Resistance: Abattoirs require flooring that can withstand extreme temperature variations, especially in areas like freezers and hot washdown zones. Tile flooring has excellent thermal stability, which means it does not crack or lose integrity when subjected to sudden temperature changes.
Durability: Tile flooring is capable of enduring not only thermal shocks but also the weight and movement of heavy machinery and equipment, making it a durable choice for the demanding conditions of an abattoir.
Cost-Effectiveness: Although the initial investment might be higher, the long-term durability and reduced maintenance costs make tile flooring a cost-effective solution for abattoirs.
How Does Stainless Steel Flooring Enhance Safety and Hygiene in High-Traffic Abattoir Zones?
Stainless Steel Flooring significantly enhances safety and hygiene in high-traffic abattoir zones through several key features:
Durability and Impact Resistance: Stainless steel flooring is exceptionally robust, making it ideal for withstanding the heavy impact and frequent movement of equipment commonly found in abattoirs. Its strength ensures it can handle high-traffic and heavy-duty use without deteriorating, maintaining its integrity over time.
Non-Porous and Hygienic Surface: The non-porous nature of stainless steel prevents liquids and organic materials from penetrating the surface. This property is crucial in abattoirs, where blood, fats, and other organic substances are prevalent. A non-porous surface significantly reduces the risk of bacterial growth and cross-contamination, essential for maintaining strict hygiene standards.
Ease of Cleaning and Sanitization: Stainless steel’s smooth surface is easy to clean and can withstand harsh cleaning agents and disinfectants used in abattoirs. This ease of cleaning ensures that hygiene can be maintained with minimal effort, as the surface can be quickly and effectively sanitized without the risk of damage.
Corrosion Resistance: In environments exposed to moisture and various chemicals, stainless steel’s resistance to corrosion is a vital feature. It withstands exposure to water, cleaning chemicals, and organic acids, maintaining its quality and appearance over time.
Slip Resistance: Many stainless steel flooring options are available with textured finishes to provide additional slip resistance. This is crucial in wet or greasy conditions often found in abattoirs, thus enhancing worker safety by reducing the risk of slips and falls.
Temperature Resistance: Stainless steel can tolerate extreme temperature variations, which is essential for areas like freezers and hot wash zones within abattoirs. Its ability to withstand these conditions without warping or cracking ensures a consistent and safe floor surface.
Aesthetically Pleasing and Modern: Beyond functionality, stainless steel flooring also offers a sleek, modern look that can improve the overall aesthetics of the facility.
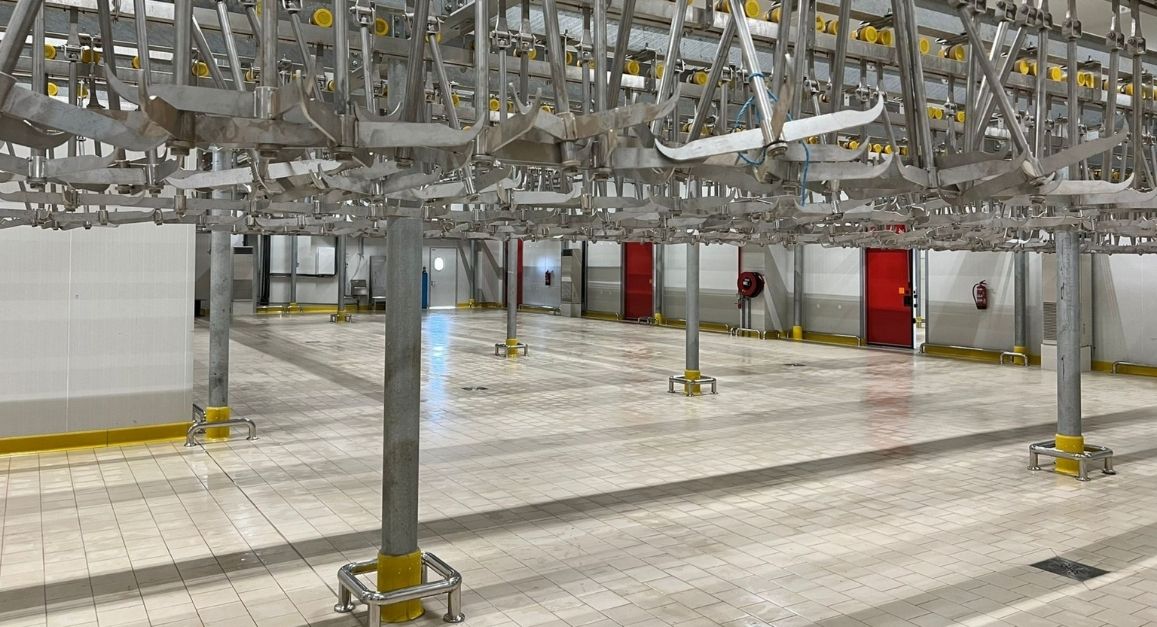
Why is Vibroser the Leading Provider of Flooring Solutions for Abattoirs and Food Processing Industries?
Specialized Flooring Solutions: Vibroser specializes in creating hygienic, hard-wearing, non-slip flooring solutions that cater specifically to the demanding needs of abattoirs and food processing facilities. Their floors are designed to withstand heavy foot traffic, exposure to harsh cleaning agents, and extreme temperature variations, all common in these industries.
Commitment to Hygiene: Understanding the critical importance of hygiene in food processing, Vibroser flooring solutions meet and exceed stringent hygiene standards. Their floors are often treated with antimicrobial agents to inhibit the growth of bacteria, molds, and fungi, ensuring a sterile processing environment.
Durable and Safe Products: The durability of Vibroser’s products ensures a long lifespan even under the rigorous conditions of meat, fish, and seafood processing. Their non-slip feature is especially vital for worker safety, significantly reducing the risk of accidents in wet or slippery conditions.
Innovative Hygienic Solutions: Beyond flooring, Vibroser also offers hygienic cold room panel protection products. These are crucial in abattoirs where temperature-controlled environments are necessary for the preservation of meat. The panels are designed to maintain cleanliness and temperature integrity in these critical areas.
Advanced Drainage Systems: Vibroser’s hygienic drainage systems are another testament to their holistic approach to abattoir design. These drainage systems are essential for efficient waste water management, ensuring that facilities remain clean and hygienic with reduced risk of contamination and water stagnation.
Global Reach and Reliability: Vibroser serves clients all over the world, showcasing their global expertise and reliability in the field. This wide reach also indicates their ability to understand and meet diverse operational requirements and standards across different countries and regions.
Cutting-edge Technology and Quality Assurance: Vibroser’s commitment to utilizing cutting-edge technology and maintaining high quality standards in their products positions them as a leader in the market. Their flooring solutions are not just practical, but are backed by research and innovation, ensuring they provide the best possible performance in demanding environments.
In summary, Vibroser’s dedication to providing specialized, hygienic, and safe flooring solutions, along with their innovative ancillary products like cold room panels and drainage systems, and their global operational capacity, make them a top choice for abattoirs and food processing industries worldwide. Their comprehensive approach to flooring and facility hygiene ensures that businesses in these industries can maintain the highest standards of cleanliness, safety, and efficiency.